10 Tips for Greater Energy Efficiency
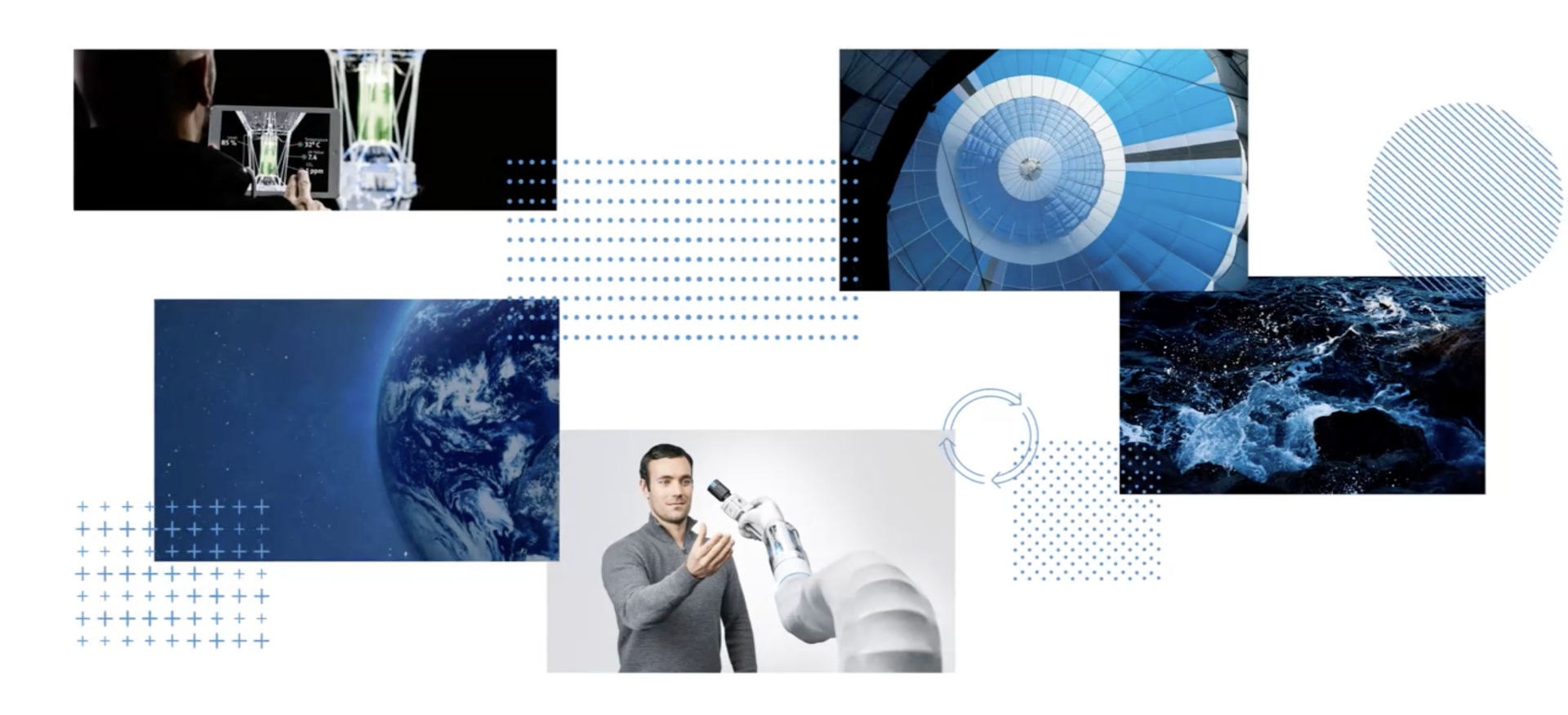
While automated systems enable manufacturers to produce goods with greater speed, flexibility and cost-effectiveness, they also consume energy. Fortunately, there are many ways to increase the energy efficiency of your equipment, taking you one step closer to achieving carbon (CO2) neutrality.
Here are 10 tips to help you reduce the energy consumption of your pneumatic, motion control and remote I/O systems.
1. Select the Right Components — and Account For Size and Weight
It’s important to match your actuator to your application. For example, single-acting cylinders or units with lower pressure on the return stroke can decrease your compressed air consumption. For longer standstill times, we recommend servo/stepper motors with holding brakes. When possible, also look to use pressure regulating plates and pressure regulators. Festo engineering tools help you to select the right product for your application.
In addition, the design of the drives heavily influences energy consumption. The smaller the actuator, the more energy efficient it is, making it important to avoid oversizing the drives. Try to also keep your moving masses as small as possible by combining components and choosing lightweight products, where possible. Following these tips can save up to 40% of your air consumption through properly sized pneumatic actuators.
2. Minimize Friction
The less friction there is, the lower the energy losses and the longer the service life. Low-friction components like our pneumatic DGSL or DGST mini slides, for example, move with precision and minimal friction. Also, be sure to service your electric drives and axes regularly to reduce frictional losses.
3. Look to Recover Energy
In many applications, electric drives have to accelerate and actively decelerate loads. You can reuse this braking energy under certain circumstances — e.g., with a DC link coupling, which makes it possible to save electrical energy.
In applications where acceleration and deceleration phases of different drives coincide, you can couple the DC links of the controllers and store the braking energy there. The motor controller CMMP-AS helps you do just that.
4. Switch Off Energy As Soon As Possible
Whenever possible, switch off the air supply. This is something you can do during machine standstills, at the end of shifts or during breaks, for example. Components, like our MSE6 module, for example, will even do this automatically.
5. Optimize Settings With Open- and Closed-Loop Control
Optimal controller settings with flat acceleration ramps will reduce energy consumption and minimize vibrations. With the + software, you can set up good control performance for axis systems with little oscillation and controller intervention.
6. Incorporate Air Saving Circuits
Maintaining constant vacuum pressure isn’t necessary to hold objects — and air saving circuits can help. For example, our OVEM and VADMI vacuum generators with intelligent monitoring only generate a vacuum when necessary and can switch off automatically, saving you roughly 60% of compressed air.
7. Reduce Pressure Level and Pressure Losses
There are different ways to reduce your pressure levels to lower energy costs. For example:
- An unnecessarily high pressure level in the entire network requires a lot of energy. Reducing system pressure by 1 bar can save up to 10% of energy.
- Some machines require a continuous minimum pressure. If applications require a higher pressure level at specific points, you can implement this capability locally with our DPA pressure booster instead of raising the pressure in the entire supply network.
To reduce pressure losses, it’s important to maintain proper compressed air treatment, which extends the life of components and systems. Check that filters are being used wisely because every filter stage reduces the flow rate and increases the pressure drop. Regularly performing maintenance and selecting the right compressed air treatment components can reduce your energy consumption by up to 20%.
8. Reduce Tube Lengths
Many tubes between valves and actuators are too long, increasing compressed air consumption through “dead volume.” This unproductive air also has a negative effect on the cycle time of the system. The dead volume in the tubing frequently accounts for a large percentage of overall consumption — especially where actuators or grippers with small volumes are involved. Pay attention to the shortest possible tube lengths and optimal tube routing. Above all, we recommend positioning the valve manifolds in a decentralized way.
9. Reduce Leakages
Leaks that remain unnoticed drive energy costs. We know from experience that the leakage rate of existing systems can be reduced by up to 20%. It is therefore important to regularly examine the compressed air system with an eye toward leak detection.
10. Monitor Compressed Air Continuously
Compressed air monitoring makes your air consumption immediately transparent. Based on the flow measurement, you can identify deviations due to leakages or pressure losses and quickly initiate the right energy-saving measures. Tools like our Festo Automation Experience (Festo AX) even use artificial intelligence to predictively calculate how the status of systems will change.
To learn more, visit our website.