Tips to Get Started in Battery Cell Manufacturing
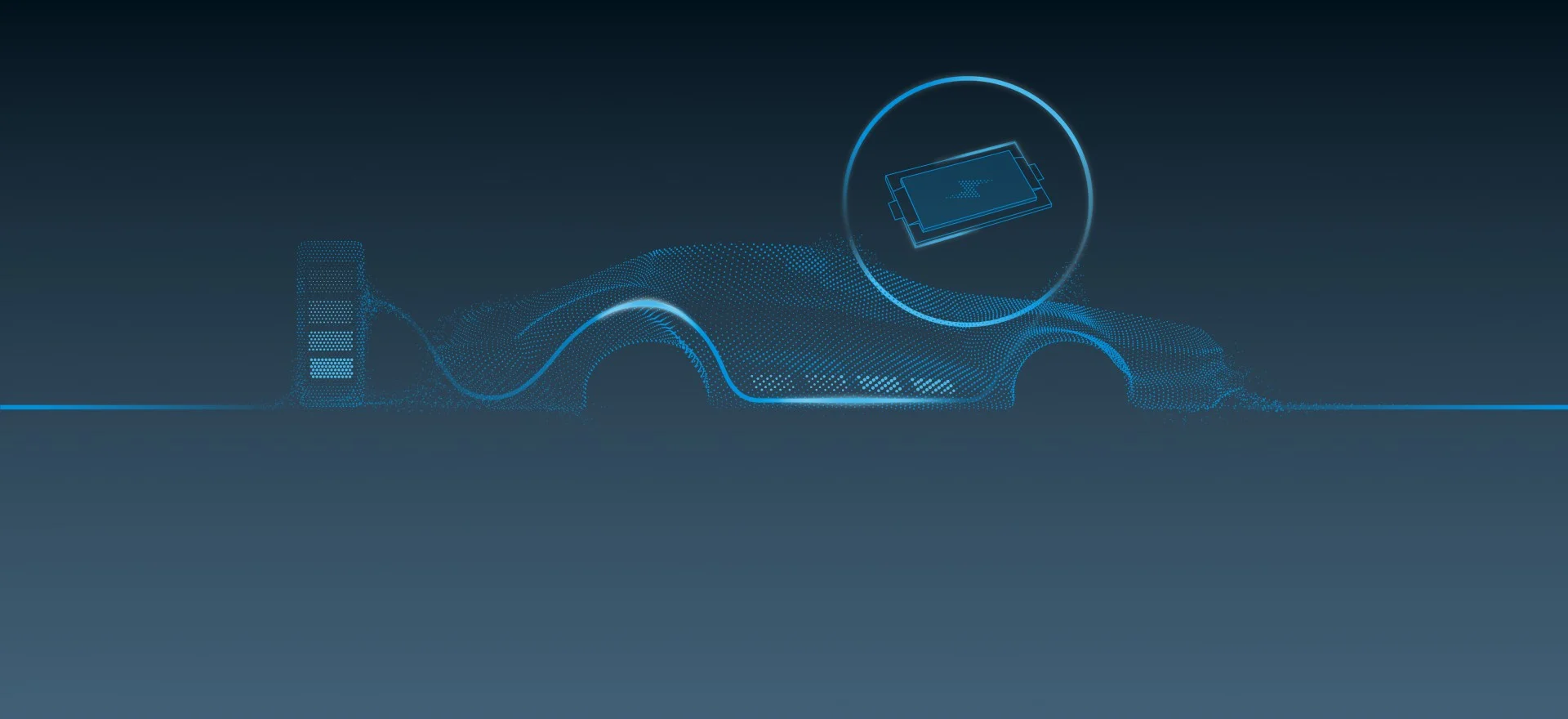
Battery cell manufacturing is on the rise, driven by the increasing demand for electric vehicles (EV), the development of renewable energy storage, and consumer electronics. These trends have opened up many exciting opportunities for companies looking to enter this space.
Yet despite its rapid revolution, battery cell production comes with its share of challenges. From selecting the proper automation components to ensuring high product quality, here are a few technical tips to keep in mind if you plan on entering this exciting industry.
Select the Right Components
The success of your battery cell manufacturing operations relies on your choice of automation components. For example, to avoid contaminating the cells, it’s important to select parts that are free of copper, nickel and zinc. These metals can trigger electrochemical reactions in the battery cells that impair their performance and service life. Contamination can also lead to micro-shorts and other faults, jeopardizing the safety and reliability of the batteries.
At Festo, we offer many pneumatic and electric automation components that support the entire battery production process. Capable of high throughput and repeatability, these products are suitable for many different process steps, including conveying, feeding, controlling aggressive media, pressing and parts handling. We also have a variety of parts free of copper, zinc and nickel, as well as cleanroom-compliant components according to ISO 14644-1.
Optimize Production Processes
Optimizing your production process is crucial to remain competitive in the booming battery cell production industry. Think about how you can carefully plan and monitor all production steps, such as raw material preparation, cell assembly and end-of-line testing. Continuous process improvements will also reduce your production costs while keeping the quality of battery cells high.
Implement Quality Control
The safety and reliability of your products rely on proper quality control. Automated testing systems ensure the accuracy and consistency of the tests. Thorough quality control not only contributes to product safety, but also reduces scrap and time-consuming rework.
Invest in Your Employees
Well-trained employees are the backbone of any successful production plant. Be sure to invest in the continuous training and development of your staff, through digital and physical training courses, to cover technical skills and promote safety and environmental awareness. A qualified team requires less training time and will recognize production problems at an early stage, leading to proactive measures that improve production processes.
Consider All the Environmental Aspects
The production of battery cells involves various environmental aspects that must be taken into account. Examples include raw material extraction, energy consumption and waste disposal. Focus on using environmentally friendly materials and processes, and implement recycling programs to minimize your ecological footprint.
Be Sure to Comply With Regulations
Compliance with legal regulations and standards is an essential part of battery cell production. These can encompass safety and environmental standards, as well as specific requirements for lithium-ion cells. By complying with these regulations, you can minimize your legal risks and gain the trust of your customers and partners.
To learn more about how to successfully plan your battery cell production application, read our expert interview with Jochen Luik, Global Industry Segment Manager Electronics at Festo.
Also, download our ebook, “The Key to the Safe Production of Battery Cells for Electric Cars,” to learn how to optimize quality and costs right from the start.