Intralogistics – 5 essential questions
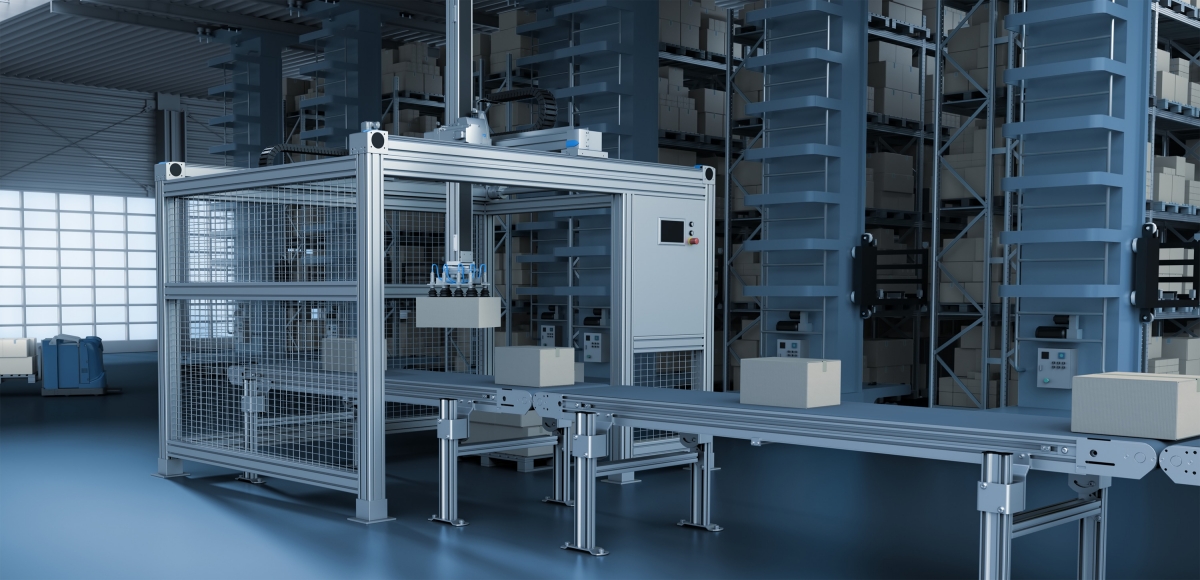
Over the past quarter century, there has been a technological revolution involving information and automation. Nowhere has that been more apparent than in distribution centers and warehouses. As one of the world’s preeminent innovators in motion automation and positioning, Festo and its machine building partners are at the forefront of Intralogistics innovations.
Frank Vanderpool, Festo’s Intralogistics Industry Segment Manager, answers five essential questions about intralogistics — the management and optimization of internal logistics processes within a facility.
Question 1: Frank, please tell us a little about yourself and your focus on automating distribution center systems.
Frank: I’ve been in the industrial automation field for almost 30 years, with varied responsibilities, including design engineering, field sales, sales management, and industry segment management.
Festo focuses on supporting intralogistics capital equipment OEMs and end users with innovative motion control solutions, ranging from traditional pneumatic motion to the latest electric motion control. Our North American Customer Solutions Center in Mason, Ohio, assists OEMs and end users with solving the problems that bring them the most pain. Then we feed this application knowledge into our new product development roundtable discussions to ensure that we are addressing the future needs of our customers.
Question 2: In distribution centers, the variety of packaging sizes and types moving along conveyors is striking. Additionally, the speed at which items must be picked, handled, and sorted automatically is remarkable. What technical challenges does this present for machine builders?
Frank: Sorting systems have existed for decades, yet they continue to evolve with new technological solutions. End users want the fastest, quietest, most accurate and reliable sorters available. There is no shortage of challenges for our customers as they strive to optimize each of these areas. Today, we might be helping customers select and design the most energy efficient pneumatic system. Tomorrow, we might be helping them improve reliability using the speed and repeatability of electric motion components. Our broad and robust product portfolio, combined with our manufacturing and North American distribution center in Ohio, gives us the ability to assist these customers with a wide variety of challenges.
Question 3: In many situations, identical products and packaging are stored in a bin, while in others there may be dissimilar shapes, sizes, weights, and packaging materials in a mixed-product bin. Many operations would benefit from automated rather than manual bin picking. What are the technical challenges in automated bin picking?
Frank: Automated bin picking seems to be simple but isn’t. I’ll focus on tasks that take place after a machine vision system has identified and located the package.
As you pointed out, bins are often filled with a variety of consumer goods in many types of packaging, in various sizes, and made from different materials. The optimal end effector, the part of the machine that must securely grasp the package without damaging it, must be appropriate to the material, size, and package configuration. For example, vacuum cups for picking a foil bag of potato chips would be ideal, while a multi-finger gripper may be the best choice for a large Lego set. Selecting how many end effectors need to be available to the handling system, engineering a reliable system for attaching and detaching various grippers automatically, and programming the machine to decide which end effector is best for the next pick poses technological challenges. Developing multi-capability grippers is a priority. And Festo is actively engaged in gripper development.
How we choose to move the end effectors is another challenge. Do we use a multi-axis articulated robot, or do we use a gantry system? We must consider the required speed, payload capacities of the motion system, floor space, movement accuracy, available utilities, and cost. All the components must contribute to a robust and reliable system that delivers minimal downtime during operation and scheduled maintenance.
Question 4: In addition to bin picking, large totes and shipping cases must be lifted onto and lowered from rack storage. Describe the automation typically used for lifting and lowering.
Frank: Most automated systems that move totes and shipping cases are part of what is called an Automated Storage and Retrieval System (ASRS). Large vertical electric gantry systems distribute the totes and shipping cases to storage locations within the ASRS. The system remembers where each load is stored for future retrieval. Pallets carrying shipping cases are often moved via conveyors or by Automated Guided Vehicles (AGVs) to pallet elevators where the pallets are stored for retrieval.
There are many different systems that need to be engineered and manufactured for grasping, sliding, bar code scanning, and lifting. These systems must automatically interact with the AGVs. It truly is a complex interaction involving machine and information.
Question 5: What is new, different, and exciting about automation in distribution centers?
Frank: One of the most exciting developments has been in high mix/low volume palletizing applications. Think of a grocery store that places a weekly order to its distribution center. Inventory managers aren’t likely to order an entire pallet of sweet potato baby food. It’s more likely the store needs a single case of that variety along with single cases of many other products. The shipping cases may have different weights and dimensions. Some of the cases may be able to withstand high weight placed upon them so they can be in the bottom layers, while other more fragile cases have to be placed higher up.
Machine builders are now utilizing AI to predict the most efficient three-dimensional arrangement of shipping cases to create a stable pallet load. These automated systems often know the size and weight of the box based on its UPC code before the case arrives at the palletizer. When it does arrive, the case is placed on the pallet stack in the most efficient position in terms of compactness and stability, as determined by the AI system.
Some of these systems have automated contingencies should the robot arm or gantry system moving the cases have a fault. The system will provide the distribution center’s team with a pack pattern diagram that allows team members to load a pallet to maintain on-time shipping and reduce downtime. When I think of the thousands of different pack pattern combinations possible and the importance of a pallet load that will not crush cases and damage products or topple over, I find these new systems amazing.
To know more about intralogistics, click here.