Analyzing the N₂ Purge Carbon Footprint in Semiconductor Fabs
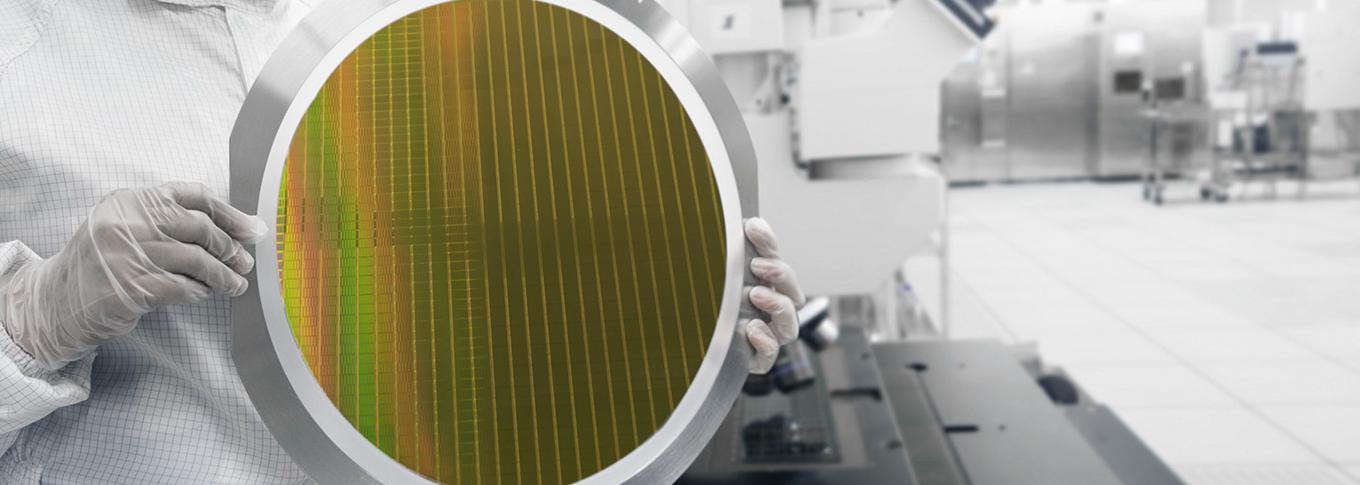
Among its many roles in semiconductor manufacturing, nitrogen (N₂) is used to purge Front Opening Unified Pods (FOUP) to create a controlled, contaminant-free environment for wafers as they are held and transported from one machine to another for processing.
In large semiconductor fabs, nitrogen consumption can reach 50,000 cubic meters per hour. In addition, a study by the European Industrial Gas Institute revealed that nitrogen production at a typical air separation plant requires 549 kilowatt-hours (kWh) per tonne of liquid N₂. Alternative nitrogen generation technology can produce the same volume of nitrogen gas with roughly half the input electricity, or 275 kWh.
And, in the United States, the electric power industry generated 4.01 trillion kWh from all energy sources, resulting in CO₂ emissions of 1.55 billion metric tonnes — an amount that translates to roughly 0.85 pounds of CO₂ emissions per kWh. When extrapolated to large semiconductor fabs with air separation systems in place, these emissions per kWh amount to roughly 5.8 x 104 metric tonnes of CO₂ per year.
These numbers make the case for energy-efficient onsite nitrogen generators, which provide ultra-pure gaseous and liquid nitrogen onsite with less than one part per billion (ppb) impurities.
Fortunately, analyzing all the areas that use nitrogen in the fab — and minimizing its usage — can yield large savings over a short time. One such area is the FOUP purge, which is shown to have many possible opportunities to use the nitrogen wisely via actively metering with closed loop control.
Piezoelectric purge valves can satisfy some of this need — and they run at extremely low power, making them a portable solution within the manufacturing line. In fact, simply deploying such a system has been shown to reduce a large fab’s nitrogen consumption, related energy use and CO₂ emissions by 4 percent each year.
The Benefits of Piezo-Based Flow Control
N₂ purge systems that use piezo technology offer greater precision, consume less power and are more energy efficient compared to flow control systems that incorporate solenoid valves. They also increase the energy efficiency of front-end manufacturing processes, improve overall sustainability and contribute to corporate sustainability goals.
N₂ purge systems unlock these benefits because the design of the piezo valve limits the size of abrasion-causing particles to about 0.1 micrometer (μm). This value — which is the N₂ purge system’s peak particle size per switching cycle — is about five times smaller than that of conventional N₂ purge systems. By preventing wear due to friction, the piezo technology also lengthens the valve’s service life, unlocking significant operational and maintenance savings.
To learn more about the role of the N₂ Purge System in reducing carbon emissions, download our white paper.