Designing a Twin Bearing System for High Loads
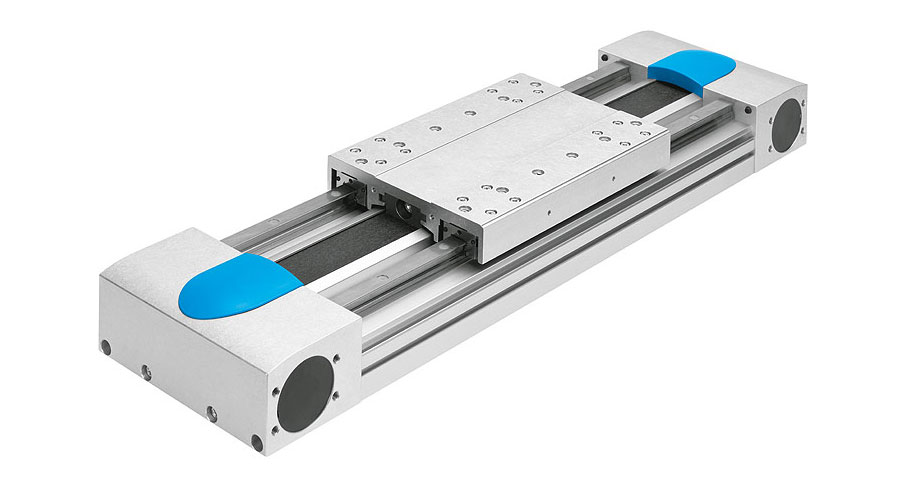
Most electromechanical guide units consist of an extruded aluminum profile, a single guide rail and caged, recirculating ball bearings driven by a motor through a belt or ball screw. While these systems have proven their success in many automation applications, they have their limits—especially where high loads are concerned.
The good news is there are alternative designs you can turn to without breaking the bank. At Festo, we designed a heavy-duty axis with a single, wider profile, multiple guide rails and a new bearing system that successfully manages high loads.
How It Works
In any dual-rail system, both axes are never completely parallel. However, in typical systems using two separate but aligned axes, the plate connecting the two bearing carriages compensates for some of the misalignment by deforming.
The issue when using a single profile is that there is hardly any compliance. Because the structure is so stiff, the bearings fight each other—resulting in premature wear and failure. To overcome these challenges, we made a few modifications to the bearing system.
Larger ball bearings compensate for misalignment. The balls we selected for our twin-rail system are slightly larger in diameter than the balls in a single-rail system. Each ball compresses slightly—compensating for small but important misalignment tolerances. Think about it this way: a football pressurized to 10 psi can be squashed or deflected more easily than a tennis ball at the same pressure.
Uncaged ball bearings create more space—and a higher contact area. While most of us assume caged ball bearings are superior to uncaged bearings, all bets are off when dealing with high loads. Most of the space inside a caged bearing carriage is utilized by the cage itself—reducing the space available for the balls. Uncaged bearings, on the other hand, provide more space for the balls and a higher contact area—translating to a higher load capacity that benefits heavy-duty applications.
Bear in mind, the maximum speed of a system with uncaged bearings will be lower than a system with caged bearings. But for an axis capable of carrying a thousand kilos, speed is hardly the primary consideration.
An “O” ball configuration distributes forces more evenly within the guide system. The orientation of the balls inside the bearing housing plays a big role in the linear guide’s ability to resist deflection.
Typically, there are two mounting geometries—face-to-face (X) and back-to-back (O). In an X-arrangement, the balls make contact with the rail in an inward-facing configuration that creates an “X” pattern inside the rail. This narrow footprint between the center lines of the balls provides greater stiffness—lowering the guide’s ability to handle moment loads. While this arrangement proves successful in single-axis systems, which have no inherent moment loads to manage, it’s too stiff for twin-guide systems.
Because O-arrangements feature an outward-facing ball orientation, the footprint between the balls is much wider. This design offers greater resistance to applied moment-based forces than the X-arrangement—improving the linear guide’s rigidity.
Once we integrated the new bearing system into our twin-rail system, we conducted six months of durability testing. We’re pleased to report there were no failures.
Learn More
There is no simple way to select the “best” bearing system—whether large or small balls, caged or uncaged, or an X versus O arrangement. Rather, it’s important to factor in your choice of guide system into the overall design, especially in systems carrying large masses.
To learn more about our heavy-duty EGC-HD twin-rail system, visit our product page.