Grippers 101: Exploring Common Robotic Gripper Types
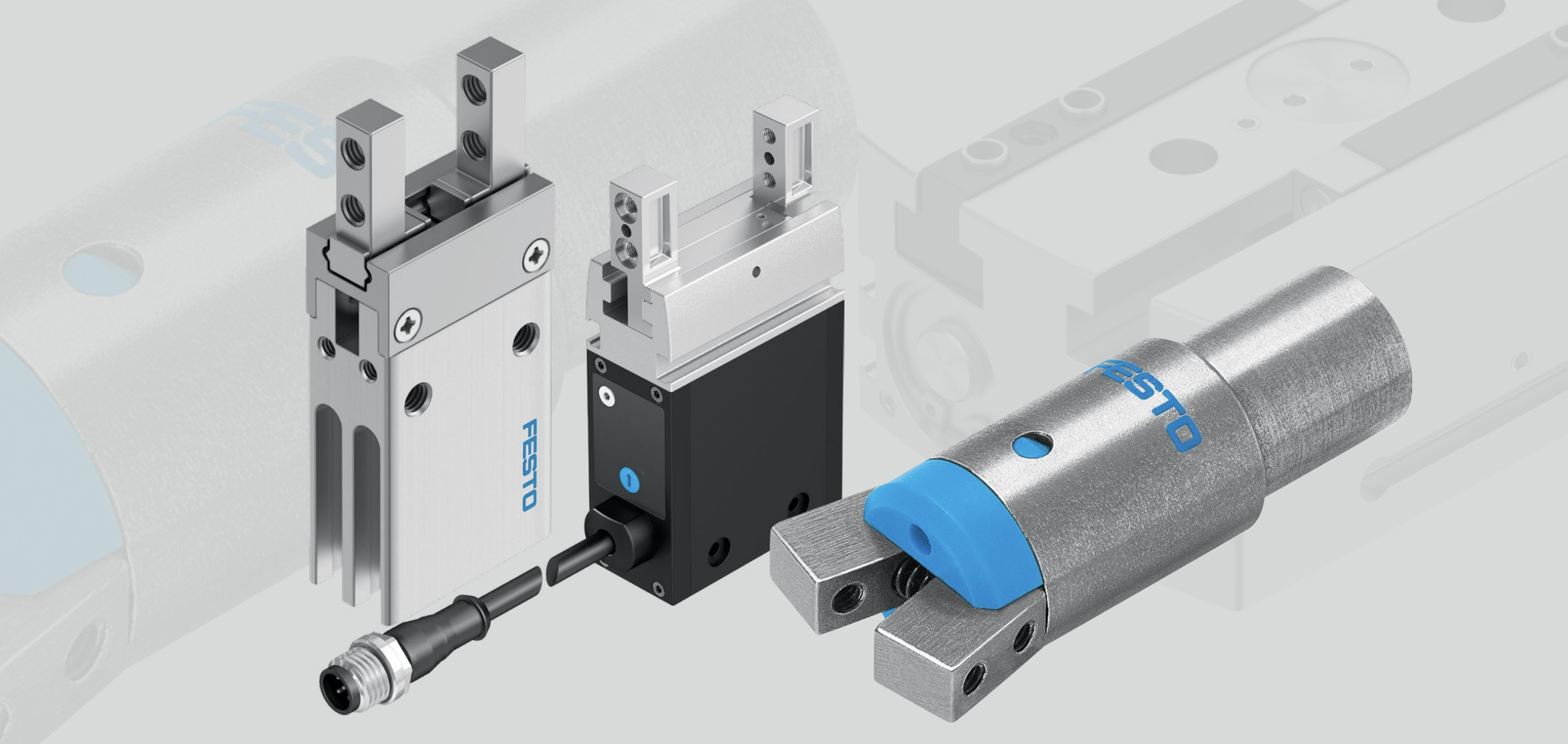
With all the robotic gripper choices in front of you, it can be a challenge to figure out which one is best for your application. Selecting the right one depends on a number of factors, including the nature of the task, operating environment, size, mass and material of the workpiece. Other important factors to keep in mind include upfront, operating and maintenance costs, as well as energy consumption. Here’s a quick rundown of some common gripper types.
Mechanical grippers make up the bulk of the market and fall into two categories: pneumatic and electric. Pneumatic grippers are lightweight, feature high grip forces and can handle fast cycle rates, while electric grippers offer greater precision, affording end-users with greater force and travel control. At the same time, electric grippers tend to increase upfront costs due to the presence of a motor and other internal components.
Whether electric or pneumatic, mechanical grippers fall into several design classes: parallel grippers, which have two- and three-finger designs; radial grippers, which open to 180 degrees; and angular grippers, which quickly open to an acute angle — e.g., 30 degrees.
Another common gripper technology is the vacuum gripper, which combines suction cups and vacuum generators. Vacuum grippers are typically more compact, lightweight, faster-acting and lower in cost compared to mechanical grippers. However, suction cups are prone to wear and commonly have to be replaced regularly. Venturi style vacuum generators consume high rates of compressed air — a fact that can be disadvantageous in applications requiring high pick rates. At the same time, the vacuum gripper’s speed and weight make it a popular choice in many end-of-arm tooling applications.
To learn more, read our ebook.