How To Reduce CO₂ Emissions With Next-generation N₂ Purge Systems
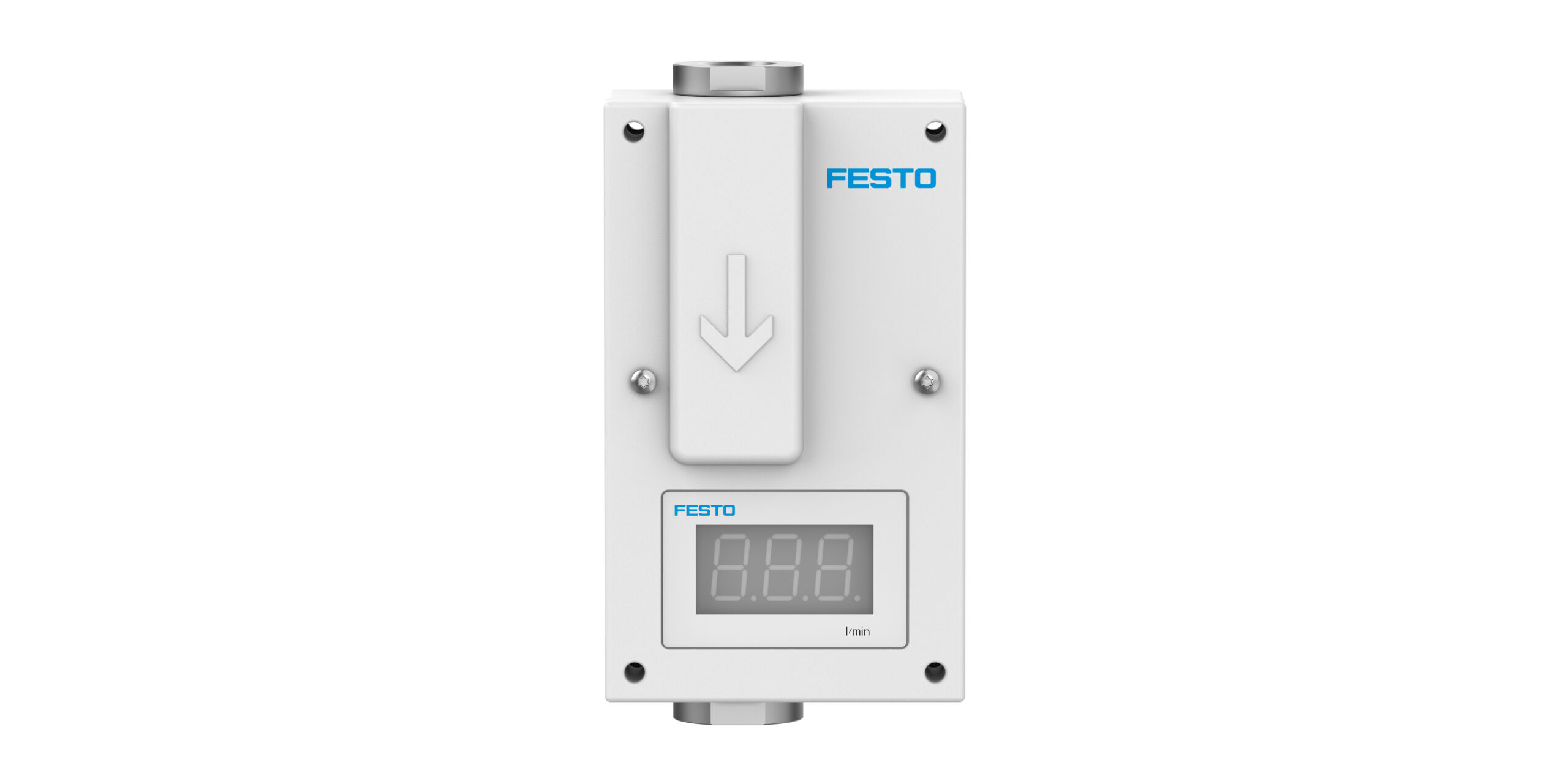
Semiconductor manufacturers face mounting pressures to reduce their energy consumption and carbon dioxide (CO₂) emissions. The push to become carbon neutral and reduce the effects of CO₂ on the climate is a gargantuan international effort. However, achieving the goals set out by climate scientists and the United Nations is no easy task for any industry — let alone the semiconductor manufacturers.
Due to the highly precise, complex nature of the chip manufacturing process, hundreds of gasses and chemicals play a role across several hundred process steps, such as thin film deposition, coating, chemical mechanical polish, lithography, metrology, baking and etching and many more.
Compounding these challenges, manufacturers must keep up with demand in a global market that is projected to hit over $1,380 billion USD by 2029.
For the average manufacturer, keeping up with such massive demand — all while implanting more transistors on shrinking chips, maintaining production yields and developing more advanced semiconductor manufacturing technologies — can make reducing energy and carbon emissions seem like an afterthought.
Fortunately, there is an easy-to-address area within the fab that can unlock tremendous energy savings, and it involves nitrogen (N₂) — the most widely used medium in the semiconductor manufacturing process.
The N₂ Purge System in Action
To operate in inert environments, semiconductor manufacturers flush the wafer pods, or front opening unified pods (FOUP), and other production equipment with ultra-high purity, particle-free nitrogen gas. This protective measure has been an industry standard for decades due to its ability to separate nitrogen from air in large amounts. At the same time, however, the compression and cooling processes involved in producing the nitrogen consume a lot of energy in order to separate the nitrogen from oxygen and other trace gasses.
Leveraging energy-efficient piezo valve technology, the Festo N₂ Purge System is ideal for FOUP storage and buffer spaces. This flow controller consists of a two-way proportional valve and integrated flow sensor, while its integrated electronics include the following:
- A power supply.
- Internal voltage control for the piezo bender.
- Stable, precise control loop for the sensor.
- Piezo proportional control valve — e.g., the Festo VEMR.
During the nitrogen purging process, the electronic system continuously controls the flow rate inline with the setpoint value. The piezo valve ensures a repeat, accurate flow rate of up to 25 normal liters per minute (nl/min) over the valve’s entire service life, with up to 30 nl/min possible in the short term.
In addition, users can monitor the pressure at the outlet of the FOUP using an additional pressure sensor — such as the Festo SPAN sensor, which works in the 10 kilopascal (kPa) range and features excellent repeatability, remote zero set function and compatibility with IO-Link, a short-distance, point-to-point communication protocol that enables data collection from sensors and actuators.
To learn more about the role of the N₂ Purge System in reducing carbon emissions, download our white paper.