An Overview of Functional Safety in the Process Industry
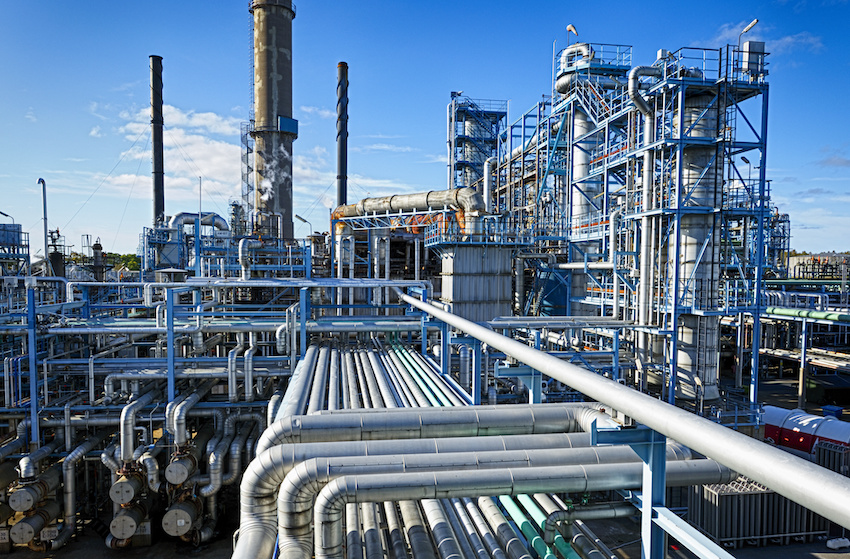
Implementing functional safety is critical in the process industries, which include dangerous chemical, petroleum and petrochemical applications. The systems in these industries, down to the lowest practical level, must be designed to reduce hazards against people, property and the environment — especially in the event of a malfunction or failure.
How to Determine and Assign SIL
An important metric for the process industry, Safety Integrity Levels (SIL) measure the safety level or risk expected for a system in terms of PFD, or the probability of failure on demand. There are four distinct levels, with SIL1 representing the lowest risk and SIL4 representing the highest acceptable risk. In general, as the levels increase, the associated safety level also increases. At the same time, the probability that the system will fail to perform properly is lower.
Typically, the system’s complexity and installation and maintenance costs increase with the levels as well. Once a level has been assigned to a system, specific installation principles, such as redundant circuit design, must be observed to minimize safety risks in the event of a malfunction.
Functional Safety Standards
The basic standard for functional safety is IEC 61508, which encompasses electrical, electronic and programmable electronic safety-related systems. It also outlines the methods for assessing safety risks using a risk graph, as well as designing suitable safety functions for sensors, logic circuits, actuators and other devices.
The standard IEC 61511 describes how to implement IEC 61508 for the process industry with a focus on applications with a low demand mode. Unlike high demand safety functions, which are expected to occur more than once a year, low demand functions have an expected demand rate of less than once a year. Any company that implements or operates a system that represents a potential hazard for employees, local residents or the environment must minimize the process risks under fault conditions. To do so, IEC 61508 and IEC 61511 outline the following steps:
- Define and assess any risks according to detailed failure probabilities for sensors, controllers, actuators and other components.
- Define and implement measures to minimize residual risks.
- Use only evaluated or certified devices.
- Conduct recurring tests to ensure compliance with safety functions.
Learn More About Functional Safety
Safety engineering is one of the most important requirements in the process industry. At Festo, we offer products and solutions that are the perfect prerequisite for implementing safety engineering as easily and cost effectively as possible.
To learn more, please download our Guideline for Functional Safety.