Tekmill Tube Handling System With Festo Gantry Improves COVID-19 Testing
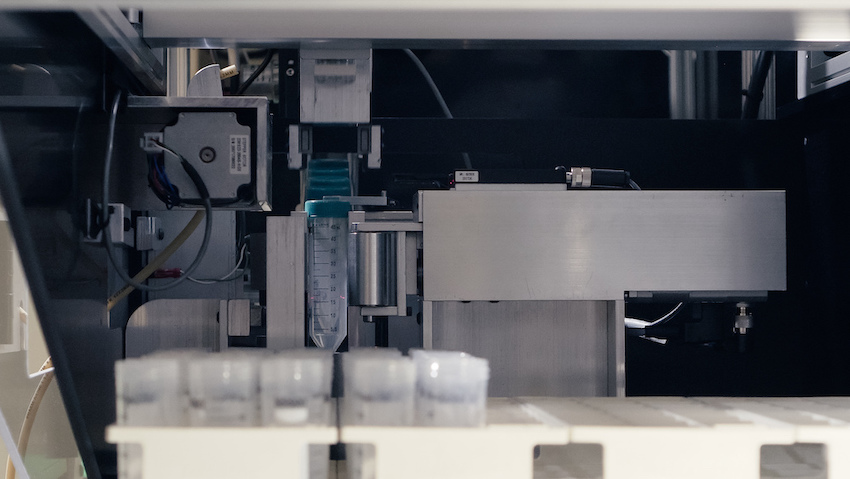
The need for fast, accurate and high-volume COVID-19 diagnostic testing presented a significant worldwide challenge since day one of the pandemic. The Center for Disease Control (CDC)’s testing protocol has relied on established Reverse Transcription Quantitative Polymerase Chain Reaction (RT-qPCR) methodologies, which involves the following workflow: A nasal swab for a RT-qPCR test is sealed in a specimen tube for processing at a screening laboratory. There, the tube’s cap is removed, and reagents are added to the tube. The solution then undergoes a series of lab processes to determine whether the swab tests positive or negative for COVID-19.
Under normal circumstances, screening laboratories can easily handle the volume of medical tests. However, during the pandemic the high volume of COVID-19 sample swabs overwhelmed the testing infrastructure. In light of these events, the one-sample-per-test-tube method had to be reexamined to accommodate the higher volumes of tests. Not only did this previous method lead to a substantial backlog, but the quantity of the consumables — including the reagents, specimen tubes and caps — was expensive and hard to come by.
The Benefits of Pool Processing
The log jam of samples, as well as the costs and supply of consumables, led many prominent laboratories to switch to a pool processing model, in which swabs from multiple people are placed in a sample tube and processed as a single diagnostic sample. If the multi-swab tube — a group of 10 people, for example — is negative, then no action is required. On the other hand, if the tube tests positive, then only those 10 individuals need to receive the more expensive rapid test that can identify positive results in under 30 minutes.
In this example of 10 swabs per specimen tube, a lab can analyze 10,000 tubes and screen 100,000 people for COVID-19 each day. When spread across the screening laboratory infrastructure, these numbers go a long way toward meeting the higher demand. At the same time, this pool process reduces the use of consumables by roughly 90 percent, making it a timely, cost-effective solution. However, handling 10,000 tubes per day — although significantly easier than 100,000 — still had its share of challenges in terms of laboratory infrastructure. Fortunately, implementing a robotic system to handle the samples offered a solution.
The Tekmill Robotic System for an Ag-Biotech Company
Tekmill, a contract design and fabrication company located at the University of Illinois, had developed an automated 50-milliliter (ml) conical centrifuge tube handling system for decapping, adding reagents to, capping and placing 50-ml specimen tubes into a standard 24-tube rack. Tekmill manufactured dozens of these systems for a large agricultural biotechnology company, and this customer was ecstatic when this automation system freed up its skilled lab workers who used to spend hours manually handling the 50-ml centrifuge tubes. Tekmill’s machine was reliable and fast with a throughput of over five tubes per minute, and it delivered the required accuracy for reagent delivery: +/- 3 percent error for volumes > 3 ml. This compact liquid handling system also included:
- A temperature-controlled reagent compartment
- Quick change-and-clean features
- Peristaltic-based pumps for sterility and accuracy
- A screen-based interface
- The Festo EXCM mini gantry robot, which raised each tube cap, lowered the cap onto the tube as the tube rotated in the opposite direction, and then placed the tube in the rack.
Revamping the Robotic System for Pool Processing
The first steps in any pooled testing process is to decap the tubes and accurately add the reagent. These steps are similar to what the Tekmill agricultural machine was already doing — just not at the projected volume of 10,000 tubes per day. With support from Festo, however, Tekmill electrical and mechanical engineers began a rapid project to revamp this robotic tube system for COVID-19 pool processing.
One of the team’s first tasks was to redesign the cap handling process. In the original machine, the Z-axis on the EXCM gantry robot used a parallel gripper to hold and raise each cap as the specimen tube rotated. The gantry would then hold and lower the cap back onto the tube after the tube was filled. In place of this process, the team designed the machine to take each cap off, drop the cap into a disposal bin and then add the reagent. Thanks to the gantry’s flexibility, the engineers made these design changes by simply changing the programming.
Adding Vision, Barcode Reading and Over-Torque Capabilities
While vision and barcode reading and tracking were not required on the earlier machine, Tekmill engineers had planned for these upgrades should they ever be requested. This pre-planning saved valuable time and effort when vision and barcode reading systems were added to the pool processing machine to track samples. The fluid handling system used for the original machine migrated seamlessly to the new one, along with the benefits of maintaining reagents in a sterile condition via the peristaltic pump.
In addition, during initial tests of the new machine, it became clear that some caps arrived over-torqued, meaning there was a possibility that the decapping process could damage the cap or tube. Tekmill engineers added torque-sensing capabilities to the machine to identify these anomalous conditions. The system would stop the decapping process and then move the tubes to a separate bin for manual opening. Doing so would preserve the integrity of the 10 samples within the over-torqued tube without stopping the overall process.
Other Tweaks
The new handling system only had to be loaded once per hour — an efficient use of lab staff. In addition, Tekmill engineers raised the per-load capacity to more than 400 conical centrifuge tubes and increased the tube rack size from 24 to 96 slots. Thanks to the flexibility of the EXCM gantry, any changes in tube speed or quantity became a matter of simple programming. Overall, these upgrades increased the machine’s throughput by roughly 20 percent.
Enabling 100,000 Tests a Day
The new automated 50-ml centrifuge tube handler for dry-swab COVID-19 diagnostic tests was given the acronym name CTF-COV-50, and the machine has since been applied to pool processing operations at numerous laboratories, including the Broad Institute of MIT and Harvard. Since March 2020, the Broad Institute has processed COVID-19 diagnostic tests for more than 130 colleges and universities, as well as Massachusetts K-12 schools.
Running around the clock, each CTF-COV automated tube handling system enables 100,000 COVID-19 tests per day utilizing the pool processing strategy and demonstrating the power of robotics to increase throughput in today’s automated laboratory environments.