Optimize Case-erecting, Loading and Sealing Processes with Electric Actuators
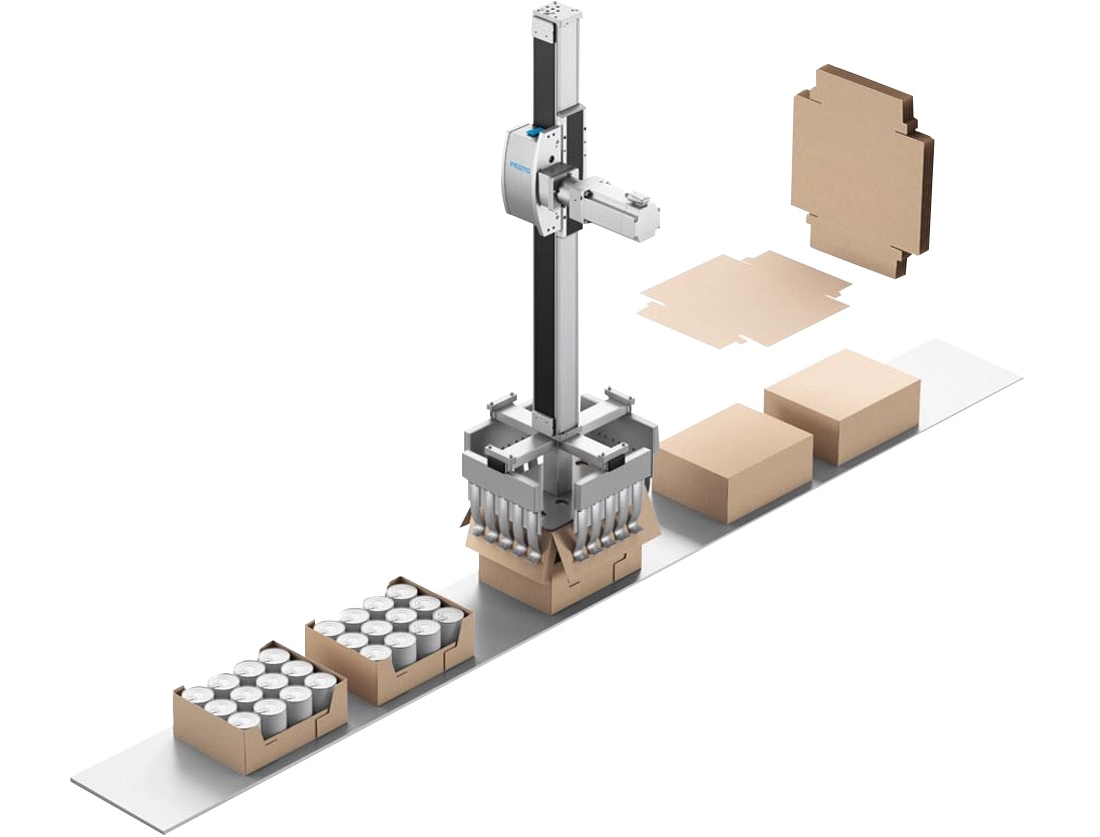
In most packaging applications, the systems that set up, load and seal cases use pneumatic actuators, which have been the industry workhorse for decades. These days, however, you have other options. For example, actuators based on electric automation (EA) are the industry racehorses that can improve your case-erecting, loading and sealing processes. Here’s how:
Coordinated Case Erecting
Efficient case-erecting systems require the solid coordination of complex electric, mechanical and pneumatic components to position, grab or open case flaps. With so many moving pieces, it can be difficult to keep spare parts on hand should a machine fail. The case-erecting process benefits from simplification, shifting reliance on standard EA components. Purchasing from our core product range, for example, enables fast delivery as these products are always in stock.
Electric actuators provide infinite adjustment ranges in the same case packer for squaring, erecting and off-loading boxes. For fast, synchronous processes in case packing and other packaging applications, decentralized I/O systems also bring feedback from digital or analog sensors and IO-Link devices to valve terminal interfaces.
Some technologies to consider include:
- ELGA or EGC rodless actuators for consistent force, positioning and velocity.
- ESBF or EPCC rod-style ball screw actuators for fine force control and positioning.
- CDPX high-performance processor panels to set and control case recipes.
- CPX-AP-I decentralized I/O system for real-time communication via gateways to IoT dashboards.
Speed Up Your Loading Processes
For loading products at high speeds, choosing the right design among 2D/3D gantry, top-mounted Delta-style and articulated arm robots is a challenge. Pick-and-place functions that load single or multiple products into a carrier with one cycle require reliability, speed and feedback from end-of-arm tooling. Although loading is often automated, pneumatic machines that use linear guidance rails require error-prone manual formatting. In selecting an electromechanical pick-and-place solution, multi-axis gantries provide a compact and cheaper alternative to complex robotics.
Our Handling Guide Online (HGO) configurator offers a convenient way to select the right gantry for your application requirements. For quick startup solutions, the Festo Motion Control Package (FMCP) includes all the necessary hardware and software — so projects that can take months with piecemeal design can be completed in a matter of weeks.
A few other loading solutions we offer include:
- ELCC.
- EXCT T-gantry.
- EGC-HD.
Case Closed
Closing box flaps is generally done by rotary devices, while gluing or taping packages is handled by end-of-arm tools. In glue applications, dispensing too much or too little adhesive is a common issue, and improperly sized end-of-arm tools can easily drive up costs due to unforeseen functions and payload requirements. Our machine vision products have all the necessary sensors to detect glue bead accuracy. For closing box flaps, our rotary actuators feature a stepper motor with encoder feedback, enabling the specific application of force to flaps within a defined time frame.
While EA solutions often have a greater price tag than pneumatic solutions, their payback is faster with increased uptime, greater manufacturing flexibility and embedded analytics. Electric actuation provides an elegant pathway to increase overall throughput and productivity without a complete redesign.
Other sealing system solutions include:
- SBSA and SBSX vision systems.
- ERMS or ERMO rotary actuators.
To learn more about how to upgrade your case packer designs, visit our landing page.