Upgrade Your Case Packing System With Electric Automation
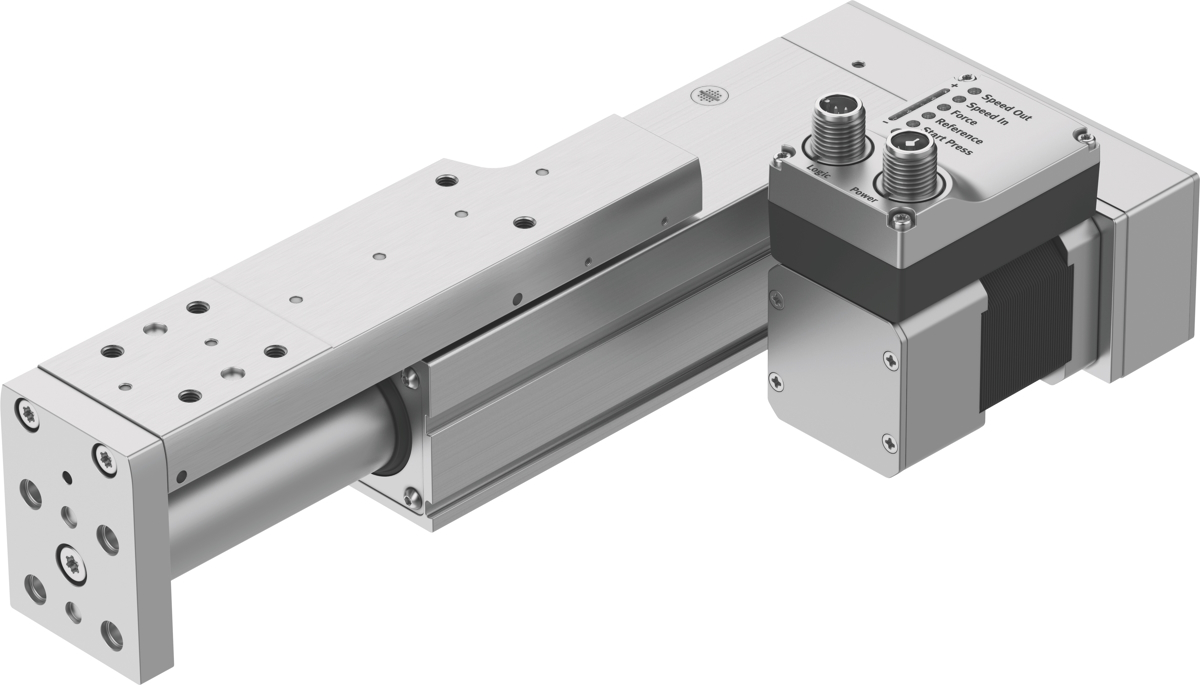
Case packer machine designs haven’t changed much over the years and still rely mostly on pneumatic actuation for many machine functions. Today, however, innovations in electric automation (EA) offer excellent opportunities to upgrade many case packing functions — including line format adjustment, collating and screening processes. Here’s how:
Simplifying the Format Adjustment Process
Format adjustments and changeover processes are necessary to accommodate different dimensions of products or cases. Pneumatic machines requiring manual measurements and repositioning of equipment take up resources and risk potential product damage. As businesses move toward fast packaging format switches and small-batch production, the agility of EA actuators is more relevant than ever.
To optimize changeovers and package formatting with consistent speed and precision, it’s a good idea to replace traditional hand cranks and manual adjustment wheels with servo-driven actuators. On-the-fly changeovers are also easier with seamless communication to third-party PLCs in I/O-Interface, Modbus TCP, PROFINET, Ethernet/IP and EtherCAT fieldbus protocols. Some technologies to consider include:
- EMMT-ST and EMMT-AS motors.
- CMMT-ST extra low voltage servo drive.
- Simplified Motion Series (SMS) Actuators.
EA Improves Collating and Accumulation Processes
In the collating and accumulation stage, case packers usually marshal boxes and contents in separate streams with conveyors or sorting machines until they come together for the loading process. While this part of secondary packaging machinery is frequently automated using pneumatics, there are still significant opportunities to increase throughput.
Pneumatic actuators can jar the products at their end strokes, taking the products out of position. And fine-tuning variable frequency drives or “across the line” gear motors running at constant velocity can result in time-based errors. Consider these application opportunities for electric automation:
- For 90-degree redirection of products on conveyors, EGC linear axes, EPCC cylinders and SMS and ELGA actuators provide fast, low-cost stepper- or servo-based control.
- SMS actuators divert or press products into organized groups with force limitations for buffering stages.
- Rodless electric actuators prevent dust ingress using stainless steel cover strips.
Better Quality Screening and Identification
Manual inspections on the production line are vulnerable to human error — especially if line speeds are fast. Many vision systems don’t have a range of detectors in a cost-efficient package and can easily drive up system cost and complexity. We developed the SBSA and SBSX vision systems — available in a simple, cost-effective package — to perform key functions in packing machines and box loading systems. A few features and capabilities include:
- Over 250 onboard programs.
- 1-5 megapixel resolutions.
- Digital I/O, serial, Ethernet IP or PROFINET communication protocols.
- Measurement, blob, object presence, barcode, dot matrix recognition and optical character recognition (OCR) capabilities.
- Integrated lighting and custom lens options.
- ISO and AIM compliance.
To learn more about how to upgrade your case packer designs, visit our landing page.